BATTERY METALS
Lithium
Lithium is in high demand as we transition to a battery-powered future, yet it's a finite resource.
From 2017 to 2022, the energy sector's demand was a key driver behind a threefold increase in overall demand for lithium, a 70% rise in cobalt demand, and a 40% increase in nickel demand. In 2022, clean energy applications accounted for 56% of total lithium demand1.
Lithium is predominately mined in Latin America and Australia, with China dominating processing. Production of lithium chemicals and products spans countries like China, Japan, and South Korea, making the supply chain global. The U.S., Australia and allied Western nations depend on factors beyond their control for the supply of processed lithium, like global prices, foreign mining and geopolitical factors.
While global lithium reserves theoretically meet rising demand, challenges exist. Few companies can produce high-quality lithium products, and expansion projects may not meet demand swiftly. Moreover, developing lithium mines takes time, with an average of 16.5 years for those starting between 2010 and 2019, however, over 80% of mining projects are often delayed2. Ensuring a stable lithium supply for the growing EV market remains a complex challenge.
The planet possesses sufficient lithium reserves for our foreseeable green-energy requirements. However, the practical process of extracting and utilizing this valuable resource remains a significant challenge.
Lithium and Electric Vehicles
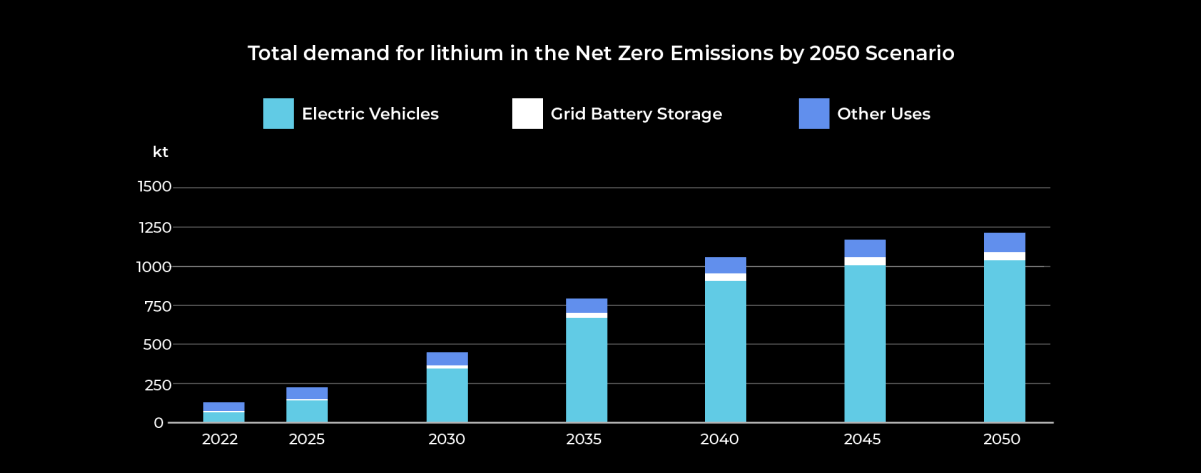
Source: International Energy Agency - Critical Minerals Market Report 2023
In 2022, electric vehicle (EV) sales surged by 60%, surpassing 10 million units, while energy storage systems experienced even more rapid growth with a doubling of capacity additions. Solar PV installations continued breaking records, and wind power was set for a resurgence after two slower years3. This incredible growth has led to a substantial rise in the demand for critical minerals.
China produces over 60% of global lithium, creating a globally reliant supply chain, even if batteries are made in the U.S. The U.S. has committed $2.8 billion in grants to expand electric vehicle battery production, part of it going to major auto suppliers, in an effort to secure domestic supply4. The American Battery Materials Initiative is another effort to ensure a stable supply of critical EV minerals. These initiatives aim to make EVs 50% of U.S. vehicle sales by 2030, spurring domestic manufacturing of EVs, chargers and batteries, aimed at making EVs affordable.
Antimony
Antimony is a silvery white, brittle solid with low electrical and heat conductivity, which exists in various forms like ingots, granules, and powder. Its abundance in the Earth's crust is estimated at 0.2 to 0.5 parts per million (ppm), and is commonly found with sulfur, lead, copper, and silver. There are over a hundred antimony minerals in nature, with stibnite (Sb2S3) being the predominant ore. The main use of antimony is as a hardener in lead for storage batteries. It is also used in alloys and solders. Antimony trioxide is crucial in flame-retardant applications for items like children's clothing, toys, aircraft, and car seat covers.
Antimony is also gaining significance as a battery metal, particularly in "liquid metal battery" technology. These batteries, utilizing calcium and antimony, are recognized for safe, reliable, and long-life stationary grid storage, crucial for achieving a net-zero energy grid by 2035.
In recent years, the U.S. and its allied nations have recognized the importance of securing critical minerals like antimony. Efforts have been made to promote domestic production, exploration of critical minerals to enhance national resilience and reduce reliance on foreign sources. Ensuring a stable antimony supply is part of a broader strategy to protect national interests and maintain a strong industrial and technological base.